- Publicado 20 feb 2023
- Última modificación 29 ago 2023
- 4 min
Hacia el Mantenimiento 4.0
Richard Jeffers, de RS, analiza cómo la tecnología está cambiando la naturaleza de la ingeniería de mantenimiento hacia un mantenimiento 4.0.
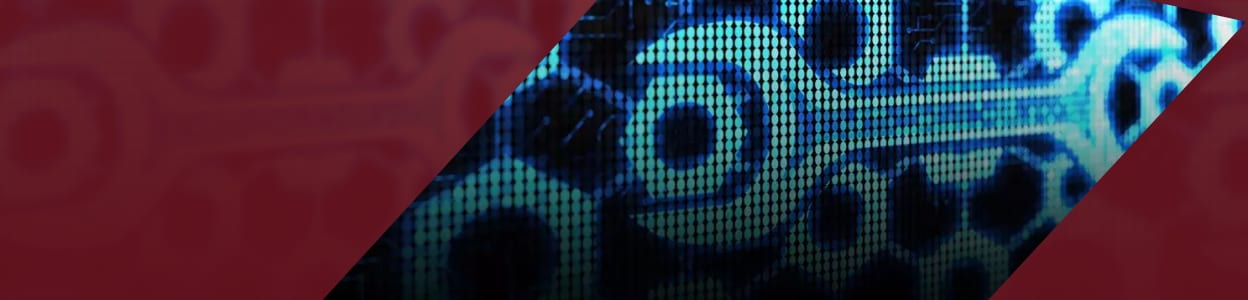
El panorama industrial de cualquier país ha cambiado por completo en el transcurso de la última generación. La mecanización dio paso a robots, que se han vuelto cada vez más autónomos. Los dispositivos inteligentes y los sensores conectados, que están integrados en los sistemas de control, implican que las instalaciones que antes requerían decenas de trabajadores, ahora son administradas perfectamente por una persona en un centro de control.
Sin embargo, cuando se trata de Mantenimiento, Reparación y Operaciones (MRO), gran parte de lo que ocurre hoy día habría sido familiar para cualquiera que trabajara en el campo hace 10 o 20 años, o incluso hace más tiempo. Algo deja de funcionar, se llama a un ingeniero para que arregle las cosas, identifican el problema, obtienen las piezas relevantes y vuelven a encarrilar todo.
Por supuesto, hay un movimiento hacia un mantenimiento predictivo más dinámico. Pero hasta ahora no hemos visto una revolución en el pensamiento de las organizaciones. Ha sido una respuesta más constante e iterativa.
Y hay una buena razón para ello. Las plantas y equipos más antiguos tienden, por su propia naturaleza, a requerir mantenimiento. Las piezas fallan, no hay forma de evitarlo. Y es mucho menos probable que los equipos más antiguos estén equipados con sensores: el Internet de las Cosas (IOT) aún no se había puesto de moda cuando se estaba construyendo una gran cantidad de maquinaria que todavía está en uso.
Si bien muchos en los negocios hablan de la Industria 4.0, el concepto aún está un tanto en su infancia en los círculos de MRO. Pero lo que estamos viendo es la expansión del Internet Industrial de las Cosas (IIoT) y un creciente nivel de interés en la tecnología que permite una mejor percepción general de la efectividad de los equipos. Un ejemplo es IO-Link, que permite extraer información del estado de sensores tontos (o no inteligentes) existentes.
Automatización gradual del mantenimiento 4.0
En algunos sectores, como el del tratamiento de aguas, una planta completa puede desconectarse por el fallo de una sola pieza, a un coste potencial de alrededor de 20.000 € por hora. Cualquier cosa que pueda evitar un costoso tiempo de inactividad no planificado como ese, debe ser digno de consideración.
Un lugar para comenzar, o investigar al menos, es aprovechar los datos de proceso existentes. Debería ser posible realizar un análisis básico de problemas pasados relacionados con el rendimiento, que pueden comenzar a mostrarle patrones de comportamiento en torno a características operativas como la frecuencia y el momento de los errores y restablecimientos.
Un análisis básico de los datos de rendimiento pasados puede comenzar a mostrarte patrones de comportamiento importantes
Richard Jeffers, director de Soluciones Digitales Industriales de RS
Modelo de predicción y prevención en el mantenimiento industrial
Dar un paso más te llevará a recopilar datos en tiempo real, a menudo utilizando dispositivos o plataformas inteligentes como IO-Link. Tan pronto como puedas comenzar a monitorizar el estado de los equipos, podrás empezar a predecir cuándo se podrían generar problemas, un salto potencialmente enorme para cualquier empresa que haya tenido problemas con tiempos de inactividad no planificados.
El análisis de los datos enviados desde un equipo revelará patrones de rendimiento; podrás ver cómo se ve el rendimiento sin incidentes en un día normal. Una vez que lo sepas, podrás detectar cualquier variación y desviación de inmediato.
Incluso puede hacer que tu maquinaria te avise cuando tenga problemas. Un ejemplo de esto es el Stack Light o AnDon Light básico, una señal muy visible de si una máquina está funcionando de manera normal o no. Los ingenieros pueden responder a las luces cambiantes marcando una máquina específica e investigando más.
Si tuviera que aislar dos palabras que creo que serán las consignas de nuestra industria en un futuro cercano, serían predicción y prevención.
Pero si bien los dispositivos inteligentes y el IIoT harán posible que las empresas pasen a un modelo de predicción y prevención, llevar eso a buen término requiere liderazgo, visión e inversión para desbloquear los beneficios de los sistemas de producción conectados y de autocontrol.
Categorías
Enlaces relacionados
- ¿Por qué aplicar un mantenimiento inteligente?
- IoT y automatización en el mantenimiento industrial
- RS apoya a ACCIONA en su camino hacia la industria 4.0
- Comprender el backlog crítico en el mantenimiento
- Medición y control del mantenimiento
- Mantenimiento
- Área de mantenimiento: Capacidad de mantenimiento básica | RS
- Soluciones de mantenimiento industrial