- Publicado 29 ene 2024
- Última modificación 31 ene 2024
- 10 min
¿Qué es el mantenimiento predictivo?
Hemos incluido una selección de las mejores prácticas de mantenimiento predictivo usadas en la industria actualmente. Detallaremos su importancia, características, ejemplos y más.
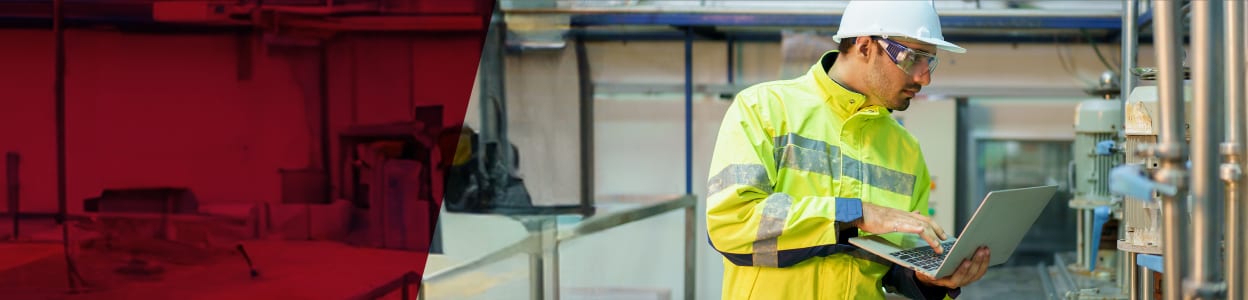
El mantenimiento predictivo es una metodología de análisis de datos que permite detectar de forma temprana y predecible anomalías en el funcionamiento o en los procesos de equipos, maquinarias e instalaciones. El objetivo es facilitar la toma de acciones antes de que se presenten fallos.
A continuación, profundizaremos en la importancia del mantenimiento predictivo, sus características, las tecnologías más comunes para la recolección de los datos que se van a interpretar, sus ventajas y ejemplos de las mejores prácticas.
¿Por qué es importante el mantenimiento predictivo?
La importancia del mantenimiento predictivo se puede resumir en dos palabras: fiabilidad y rentabilidad.
Es más rentable poner un equipo, maquinaria, sistema o instalación fuera de servicio antes de que se presente un paro súbito e intempestivo. Este tipo de paradas pueden suponer un riesgo elevado para usuarios y empleados, además de un alto coste en pérdidas materiales.
La tendencia en el mundo industrial en los últimos años hacia el mantenimiento predictivo se debe a las mejoras en sensores y otros dispositivos, el desarrollo de conceptos como el Internet de las Cosas (IoT) y la ciencia de datos (data science), por ejemplo. Esto permite un monitoreo constante de equipos y maquinarias, y el manejo de los datos permite aplicar metodologías de mantenimiento predictivo y obtener resultados muy precisos.
La diferencia básica entre el mantenimiento preventivo y predictivo consiste en que el primero se rige por el tiempo que ha estado el equipo en servicio y, normalmente, viene determinado por el fabricante del equipo o maquinaria. Se basa en promedios, bases de datos históricos y estadísticas de funcionamiento.
En el caso del predictivo, el mantenimiento se decide en base a los resultados de las inspecciones y parámetros medidos y monitorizados.
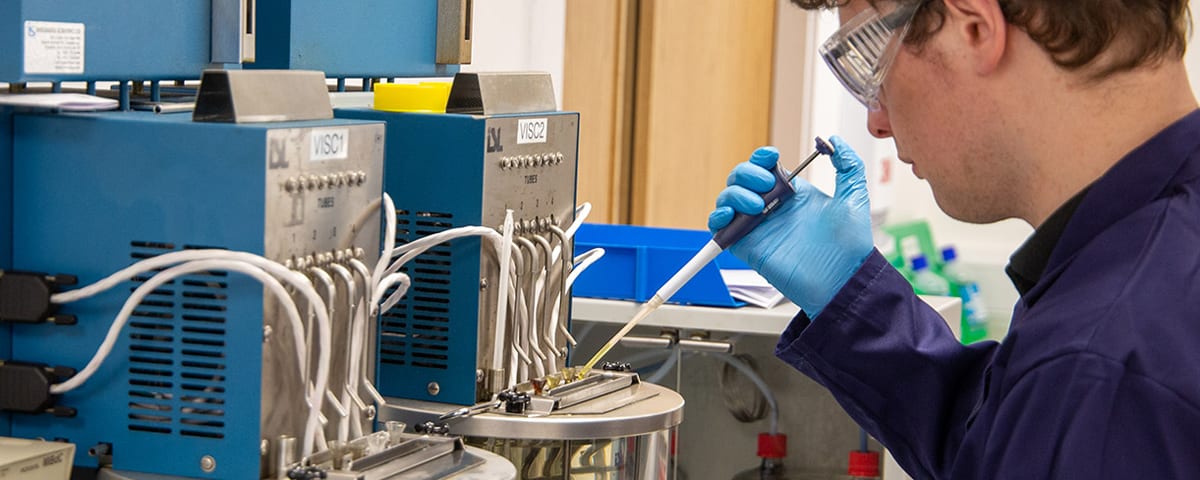
Más características del mantenimiento predictivo
El mantenimiento predictivo se caracteriza por lo siguiente:
- Persigue la optimización de los planes de mantenimiento.
- Al basarse en el análisis y desarrollo de modelos en función de datos estadísticos, se trata de un proceso altamente dinámico y reactivo, generando alertas en base a los cambios en las condiciones de integridad mecánica de los diferentes elementos.
- El hecho de poder predecir una posibilidad de fallo con antelación permite programar la compra de repuestos y partes, evitando incurrir en costes por compras de emergencia.
- Requiere personal altamente cualificado y certificado en las metodologías de inspección e interpretación de los datos medidos.
- El manejo inteligente de los datos generados permite optimizar y hasta automatizar el proceso de toma de decisiones.
Tecnologías empleadas en el mantenimiento predictivo
El mantenimiento predictivo eficaz utiliza una combinación de métodos para recopilar y analizar datos de los equipos, sistemas o maquinarias. Estos datos pueden provenir de diversas tecnologías, como sensores, instrumentos de inspección por ultrasonido, análisis de vibraciones o imágenes como las generadas por termografía infrarroja, por ejemplo.
Análisis de aceites
En este análisis se determinan diversos parámetros para obtener una aproximación de la condición de integridad mecánica de componentes como rodamientos, mesas o guías (entre otros), en los que se requiere una película de aceite para minimizar el efecto de la fricción.
El fabricante recomienda qué tipo de análisis debe realizarse, aunque normalmente consiste en determinar el grado de acidez o basicidad, contenido de agua, viscosidad, densidad y contenido de partículas.
Otros análisis más detallados pueden arrojar información de la composición química de las partículas para una mejor predicción. Son sumamente importantes, ya que la detección temprana de contaminación por agua es el factor de daño común más perjudicial.
Termografía infrarroja
Por medio de esta tecnología se puede medir de forma muy precisa la temperatura en diversas superficies, lo que permite identificar las zonas más calientes y posibles anomalías térmicas generadas por diversos orígenes según el sistema.
Estas pueden deberse a elevados coeficientes de fricción en sistemas mecánicos, a una conexión eléctrica defectuosa o mal apretada o a escapes de fluidos (tanto fríos como calientes) en sistemas de intercambio de calor, entre otras causas. Es una de las tecnologías más versátiles y su uso está muy extendido en el campo del mantenimiento industrial.
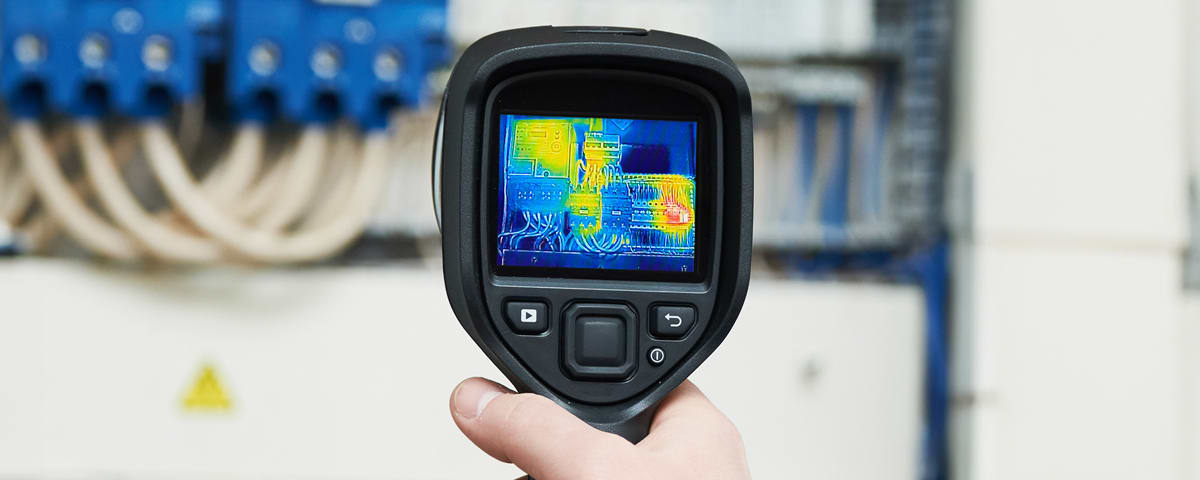
Análisis de vibraciones
El análisis de vibraciones puede considerarse una de las técnicas más empleadas y de mayor difusión en el mantenimiento predictivo.
Una vibración es un movimiento oscilatorio de pequeña magnitud. Toda maquinaria posee un cierto rango tolerable de vibraciones y, por encima de un determinado umbral, puede decirse que existe una desviación. Esta puede tener diferentes orígenes, como una lubricación inadecuada o instalación incorrecta, entre otras.
Para realizar estos análisis contamos con métodos variados, por ejemplo:
- Dominio de frecuencia: se utiliza para caracterizar las vibraciones de una máquina en función de su frecuencia a través de la transformada de Fourier, que descompone la señal de vibración en sus componentes sinusoidales de base. Con esta técnica se identifican problemas de resonancia, desequilibrio y desalineación, y las características de las máquinas como su amortiguamiento y rigidez.
- Análisis modal: se utiliza para determinar las propiedades modales de una máquina, como sus frecuencias naturales, modos de forma y amortiguamiento. Para esto, la máquina se estimula mediante una señal conocida y se mide su respuesta. Esta técnica es útil para identificar problemas como defectos en los componentes, fatiga y corrosión. Además, se usa para mejorar los diseños y el funcionamiento de las máquinas.
- Dominio de tiempo: se utiliza para caracterizar las vibraciones de una máquina en función del tiempo, con un analizador de vibraciones que registra la señal de vibración en un lapso de tiempo. Es útil para identificar problemas como desgaste y otros problemas que causan cambios en la forma de la onda de vibración. Detecta anomalías en el funcionamiento de las máquinas.
- Medición de fase: se utiliza para medir la diferencia de fase entre dos señales de vibración, con sensores en dos puntos diferentes de la máquina para registrar estas señales. Esta técnica es útil para identificar problemas de desalineación y acoplamiento entre componentes.
- Onda de tiempo: la onda de tiempo es una representación de la señal de vibración a lo largo de un período de tiempo. Proporciona información sobre la forma de la señal de vibración, para identificar problemas de desgaste, desajustes, etc.
La importancia de realizar un análisis de vibraciones se debe a que cada defecto de origen mecánico genera un patrón de vibración único. Este comportamiento típico permite puntualizar con un alto grado de precisión la causa del fallo.
Inspección por ultrasonido industrial
El ultrasonido industrial es una técnica que utiliza ondas de una frecuencia específica para detectar defectos o discontinuidades en el interior de un material.
Este sonido no se transmite por el aire, sino por los materiales sólidos de diferentes propiedades acústicas.
El análisis de la señal generada por estas ondas permite determinar con detalle el tipo de discontinuidad, tamaño, morfología, orientación y extensión.
Sus aplicaciones son variadas: calidad de soldaduras, medida de corrosión, defectos de fundición, entre otras. Y ha desplazado en muchas aplicaciones a la radiografía industrial, en el caso del PAUT o ultrasonido de arreglo en fase.
Una variante de esta inspección es la detección de fugas de aire comprimido. Una gran cantidad de instalaciones de manufactura y fabricación emplean sistemas neumáticos de aire comprimido para dotar de potencia a herramientas y equipos varios. Es por ello que una pérdida de aire presurizado puede resultar costosa incluso en un corto periodo de tiempo. Para evitar que ocurra se emplean detectores ultrasónicos especiales, diseñados para percibir frecuencias no audibles para el oído humano que se generan al haber un escape.
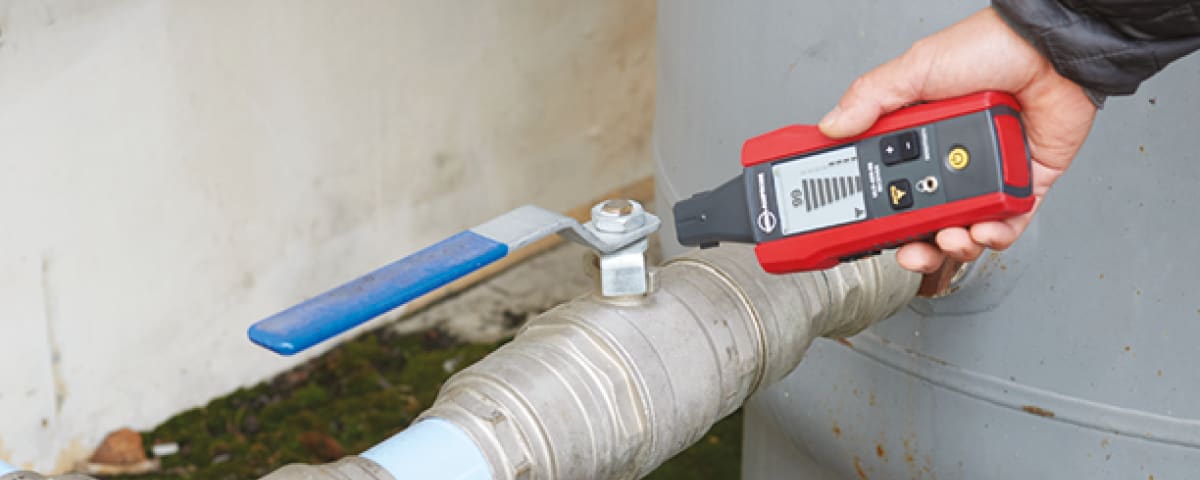
Inspección por partículas magnéticas
Es una técnica convencional, que ofrece buenos resultados en detección de discontinuidades superficiales en materiales ferromagnéticos, a bajo coste.
Consiste en aplicar un campo electromagnético a la pieza o componente que se va a inspeccionar. Luego se esparce uniformemente en la superficie un polvo de metal muy fino, que se concentra en puntos en que un defecto (como una grieta o cavidad) genera una anomalía en el campo magnético.
Ventajas del mantenimiento predictivo
Las ventajas del mantenimiento predictivo son numerosas, por ejemplo:
- Reduce el número de averías.
- Reduce el tiempo total de paradas al disminuir el número de intervenciones a través del ajuste de la frecuencia de los mantenimientos.
- Reduce los costes asociados, como el mantenimiento en sí, la adquisición de repuestos, las primas de seguros o la materia prima, entre otros.
- Permite la detección temprana de comportamientos anómalos, con técnicas como el análisis de vibraciones o la termografía infrarroja.
- Prolonga la vida útil de los componentes e instalaciones.
- Aumenta la disponibilidad real de los componentes e instalaciones.
- Incrementa la fiabilidad.
Ejemplos de mantenimiento predictivo
Como ejemplos de mantenimiento predictivo podemos mencionar:
- La termografía infrarroja a transformadores de alta tensión para detectar la presencia de concentración de puntos con alta temperatura que puedan generar un problema.
- El análisis de aceites a equipos de compresión de gas, motores de buques, motoniveladoras y otra maquinaria industrial similar, como camiones de carga pesada.
- El análisis de vibraciones en turbinas de aviones, motores eléctricos usados en diversos sistemas (como los de bombeo de crudo), motores de ventiladores o sistemas de compresión de aire o gas.
Las prácticas de mantenimiento predictivo que hemos enumerado son solo un breve resumen de todo el espectro de herramientas disponibles.
El universo del mantenimiento predictivo es muy amplio, y en él, el manejo del historial de mantenimiento o backlog es una pieza fundamental para una adecuada gestión de los activos.
Como desventajas del mantenimiento predictivo podríamos hablar de la alta inversión inicial que puede suponer tanto la instalación de los sistemas de monitorización como la adquisición de los equipos o, incluso, la contratación a terceros de servicios especializados, como la termografía o el análisis de aceite.
Asimismo, la contratación de personal certificado y cualificado en esta área es difícil, ya que la demanda es muy alta. No obstante, seguirá siendo un estándar que continuará su evolución en las próximas generaciones.
Enlaces relacionados
- Medición y control del mantenimiento
- Área de mantenimiento: Capacidad de mantenimiento básica | RS
- Comprender el backlog crítico en el mantenimiento
- Mantenimiento mecánico industrial | RS
- Estrategias de mantenimiento preventivo industrial
- Riesgos químicos en la industria
- Lubricación y limpieza de equipos en la industria alimentaria
- Mejoras de eficiencia energética en la fabricación de equipos